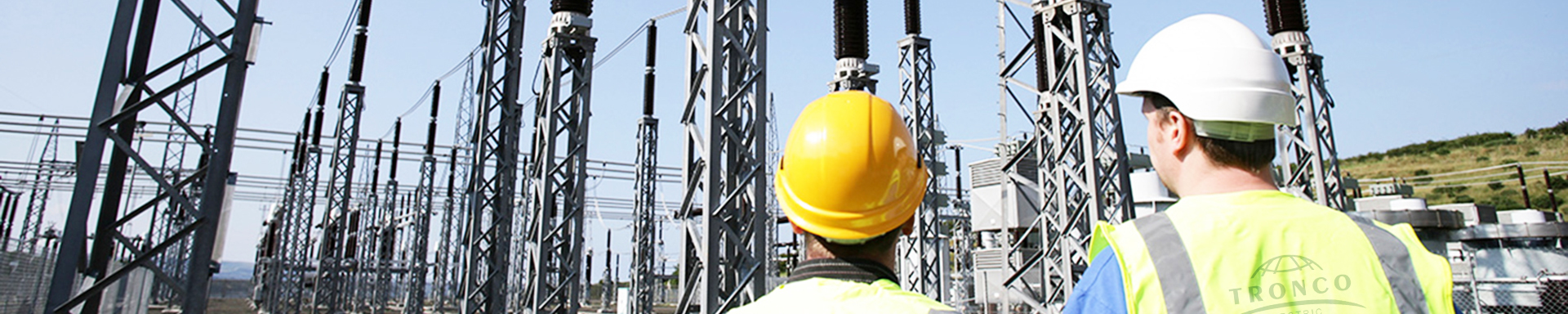
Fabricación de aisladores de vidrio templado de alta calidad
2022-11-07 20:28La calidad es una medida de excelencia y se compara en la industria de la energía eléctrica utilizando una variedad de estándares nacionales o internacionales como ANSI, IEEE, IEC, ASTM, etc. Si bien el cumplimiento de estos estándares es fundamental, la mayoría ha llegado a reconocer que los estándares estos días han llegado a representar solo los requisitos mínimos de rendimiento en una aplicación. Por esta razón, tanto los fabricantes como los usuarios buscan diferenciar aún más la calidad del producto utilizando especificaciones mejoradas. La calidad también tiene que ver con la fabricación. En este sentido, los estándares y la mejora continua de procesos se centran en los controles y la repetibilidad con el objetivo de cero defectos. En última instancia, la calidad tiene que representar la capacidad y la longevidad del producto, además del cumplimiento de las normas básicas y las especificaciones del cliente.
Se puede considerar que la fabricación de aisladores de vidrio templado consta de dos pasos clave: fabricar la cubierta de vidrio y luego ensamblar los accesorios metálicos en esa cubierta. La producción requiere equipo especializado y solo unos pocos fabricantes en todo el mundo tienen los recursos y la experiencia para llevar a cabo ambos pasos en una sola instalación de producción. En este sentido, es útil estudiar la calidad no solo en lo que se refiere a la fabricación de la cubierta de vidrio templado, sino también durante el montaje final del aislador.
La carcasa de vidrio templado constituye el aislante real. Si bien el ensamblaje del accesorio y su cementación también son importantes, esta cubierta debe permanecer intacta durante toda la vida útil para garantizar la funcionalidad del producto. Además, una vez ensamblados, la ocurrencia de roturas de la carcasa no causadas por algún evento externo debería ser rara. Por ejemplo, la expectativa general de la industria es que menos de 1 de cada 10 000 unidades instaladas por año se rompa espontáneamente. Como tal, la incidencia de la autodestrucción es un aspecto de la fabricación que la fábrica debe esforzarse por minimizar.
Además de la carcasa crítica, los componentes de hardware de un aislador de vidrio templado incluyen:
1. Gorras
La tapa en la parte superior es un accesorio de casquillo de hierro dúctil galvanizado y ensamblado con un pasador de bloqueo de acero inoxidable.
2. Alfileres
El accesorio de pasador inferior es una conexión de bola de acero forjado que ha sido galvanizada y recubierta con alquitrán bituminoso. También se puede agregar un collar de zinc de sacrificio para un rendimiento prolongado, especialmente en entornos de servicio severo.
Los accesorios de horquilla/lengüeta a veces se usan a voltajes más bajos.
3. Vidrio crudo y horno
La fabricación de la cubierta de vidrio comienza con materias primas e ingredientes clave, que incluyen sílice, alúmina, carbonato de sodio, sulfato de sodio, piedra caliza, potasa y dolomita. El vidrio de desecho (a veces denominado vidrio de semilla) es vidrio reciclado de una fabricación anterior y se agrega a estas materias primas para garantizar la consistencia de un lote a otro. La mezcla de estos materiales es específica de cada fabricante y presenta variaciones menores en los elementos que se extraen de fuentes locales o se utilizan en el horno. Estas variaciones naturales en los minerales explican la ligera diferencia observada en el tono de la cubierta aislante de vidrio.
Los hornos suelen ser de gran escala con una capacidad superior a las 100 toneladas. Para mantener la consistencia, es importante mantener la temperatura y también monitorear regularmente la química de la salida, así como la mezcla de materias primas que se alimentan. El horno es la primera fuente posible de inclusiones: imperfecciones en el vidrio que eventualmente pueden causar desmoronamiento espontáneo. Por ejemplo, con el tiempo, los ladrillos refractarios pueden comenzar a desprenderse del material en la mezcla de vidrio. Por lo tanto, los hornos deben apagarse para mantenimiento cada pocos años y volverse a revestir.
Formación de Shell
Esto se lleva a cabo en una prensa automatizada con una cantidad precisa de gota de vidrio fundido insertada en la cavidad del molde y prensada (ver Fig. 1). Las dimensiones de cada carcasa en particular, es decir, la altura y el diámetro, están definidas por estándares, pero la geometría y el perfil de la carcasa pueden diferir de un proveedor a otro.
Proceso de endurecimiento
Después de la formación, la cubierta pasa por un proceso especial mediante el cual se transfiere de la prensa a una línea de endurecimiento, pasando por un horno de homogeneización para mantener el vidrio a una temperatura alta constante. El endurecimiento del vidrio se logra enfriando rápidamente el vidrio caliente usando aire comprimido en lugares clave a lo largo de la carcasa para lograr un enfriamiento uniforme. Esto da como resultado que el vidrio tenga una temperatura central caliente pero una superficie relativamente fría. La estructura de vidrio después del endurecimiento ve el centro en tensión mientras que la superficie está en compresión y esto aumenta la resistencia mecánica y eléctrica, así como la durabilidad de las partes aislantes de vidrio. Lograr una alta calidad uniforme en este paso crítico requiere un proceso de manejo de materiales altamente automatizado y cuidadosamente controlado.
Ciclo Térmico
Después del endurecimiento, las cubiertas se transfieren a través de un ciclo térmico prescrito, donde se someten a un choque térmico con el objetivo de extraer las cubiertas potencialmente defectuosas. Las cáscaras se calientan a aproximadamente 300 °C y luego se dejan caer en agua fría, lo que reduce efectivamente la temperatura del vidrio a 120 °C. Las carcasas de vidrio endurecidas insuficientemente colapsarán debido al choque térmico repentino. Cada capa se prueba térmicamente al menos una vez y, si es necesario, se puede repetir todo el proceso. El ciclo de choque térmico es esencialmente un control de calidad clave en la medida en que cualquier caparazón que revienta es un"No vayas"mientras que las conchas que sobreviven son un 'Go'. Esas cubiertas de vidrio que colapsan durante el ciclo térmico se reciclan, los fragmentos se recolectan y se vuelven a agregar al proceso de producción en forma de vidrio de desecho (vidrio de semilla).
El funcionamiento del horno es"24/7"y por lo tanto más rápido que el proceso de montaje. Por esta razón, las carcasas terminadas se mantienen en stock hasta que estén listas para ensamblarse. Ensamblaje de la tapa y el pasador Las carcasas de vidrio se cementan en las tapas, mientras que el pasador y las camisas de zinc se cementan en la carcasa con cemento de alúmina. Aquí nuevamente, la automatización se utiliza para garantizar una cantidad de cemento medida con precisión y lograr una tolerancia de longitud precisa. A continuación, el conjunto cementado se cura ciclando a través de un baño de agua de una hora de duración a unos 70 °C. Después del curado, cada aislador de vidrio templado se somete a pruebas de rutina eléctricas y mecánicas, así como a controles visuales finales.
Prueba eléctrica de rutina: descarga disruptiva continua durante 4 minutos,
Prueba mecánica de rutina: realizada al 50% de la calificación SML para>3 seg.
Luego se realizan pruebas de muestreo en cada lote ensamblado de aisladores. Esto incluye la verificación de todas las dimensiones críticas, el cumplimiento del calibre de bola/socket, la verificación del sistema de bloqueo, la verificación de galvanizado, la prueba de M&E y la prueba de punción por impulso.
Informes de validación y prueba
Los aisladores terminados están sujetos a pruebas de diseño o calificación según los estándares de la industria, incluidos ANSI C29-2B, IEC 60383, CSA-411-1-16 y GOST 6490-93. Los clientes también pueden agregar criterios de prueba adicionales por encima y más allá de estos estándares a sus especificaciones para calificar aún más el rendimiento final del aislador.
Los informes de prueba para cada diseño de aislador deben ser específicos para la fábrica donde se fabrica el aislador. Si un proveedor tiene dos fábricas que producen el mismo tipo de aislador, debe haber informes de calificación/diseño separados para cada aislador específico de la planta donde se fabricó. Para los productos ensamblados en otro lugar, los informes de prueba para estos deben incluir referencias a la fábrica que fabricó la carcasa. Si las carcasas de vidrio templado provienen de dos fábricas, eso debería dictar informes de prueba separados (es decir, específicos de la fábrica que fabricó la carcasa).
Conclusiones
Al considerar la calidad de un aislador de vidrio templado, la evaluación y la calificación deben ser minuciosas e incluir todos los aspectos de la producción. Debe prestarse especial atención al lugar donde se fabrica la carcasa de vidrio templado y también a cómo se mantiene ese proceso para evitar que se utilicen carcasas defectuosas en el ensamblaje de aisladores terminados. Esto se debe a que, si bien el ensamblaje de la tapa y el pasador es importante, la calidad de la carcasa de vidrio templado tendrá un mayor impacto en el rendimiento del aislador a largo plazo. Los informes de prueba deben ser específicos de la fábrica en la que se produce el aislador, pero también deben hacer referencia al lugar donde se fabricó la carcasa. Esto requeriría marcas específicas de fábrica. Como mínimo, la carcasa de vidrio templado debe tener marcas moldeadas en su cuerpo, incluida la calificación de M&E, la referencia del código de lote, e identificación de fábrica (ID). Estas marcas deben ser legibles y permanentes. La identificación de la fábrica donde se ensambla el aislador debe estar marcada en la tapa del aislador, también legible y permanente. Incluso cuando se fabrica en la misma fábrica, tener tales marcas tanto en la carcasa como en la tapa ayuda a identificar cuándo se fabricó la carcasa y cuándo se ensambló. Agregar marcas de identificación de fábrica a la carcasa es simple, con poco impacto en el costo del producto, pero brinda un mayor nivel de garantía de calidad para los aisladores. Los diversos estándares de la industria (p. ej., ANSI, IEC, CSA) no solicitan específicamente la identificación de fábrica en un caparazón, pero tal vez deberían hacerlo. Incluso cuando se fabrica en la misma fábrica, tener tales marcas tanto en la carcasa como en la tapa ayuda a identificar cuándo se fabricó la carcasa y cuándo se ensambló. Agregar marcas de identificación de fábrica a la carcasa es simple, con poco impacto en el costo del producto, pero brinda un mayor nivel de garantía de calidad para los aisladores. Los diversos estándares de la industria (p. ej., ANSI, IEC, CSA) no solicitan específicamente la identificación de fábrica en un caparazón, pero tal vez deberían hacerlo. Incluso cuando se fabrica en la misma fábrica, tener tales marcas tanto en la carcasa como en la tapa ayuda a identificar cuándo se fabricó la carcasa y cuándo se ensambló. Agregar marcas de identificación de fábrica a la carcasa es simple, con poco impacto en el costo del producto, pero brinda un mayor nivel de garantía de calidad para los aisladores. Los diversos estándares de la industria (p. ej., ANSI, IEC, CSA) no solicitan específicamente la identificación de fábrica en un caparazón, pero tal vez deberían hacerlo.